Indicators on Why is Kaizen important for your business to improve You Need To Know
Some Known Factual Statements About Learn How to Apply Kaizen Habits - Medium
In business, nothing is best. That is why embracing the principle of is a smart concept. Japanese for "modification for the better," Kaizen is understood as a method of constant small enhancements with time. Source isn't a real tool, however a frame of mind. When utilizing this approach, you can apply the numerous Six Sigma tools depending upon what aspect of your business you wish to improve.
Kaizen involves everybody in the company; due to the fact that everyone is a specialist in their department, each person can identify where the gaps are and where enhancements are required. It used to be that many companies would have management sit behind their desks, composing out new protocols without having a concrete concept of what would really work in their organization.
Kaizen Business Solutions - Home - Facebook Things To Know Before You Buy
Due to the fact that these protocols weren't based upon any concrete proof, more waste was being generated. Time and materials were being squandered, not to point out creating a dissatisfied workplace. Attempting to keep up with new procedures without rhyme or reason can reduce employee morale and eventually performance. With Kaizen activities in place, management can keep continuous communication with the whole staff and listen to their ideas.

How to Use Kaizen to Continuously Improve Your Business - Tallyfy
Utilize it with the goal of improving efficiency, reducing waste, and overall security. Over time you will see the results in: Client satisfaction, Improved issue resolving amongst personnel, Greater quality product/service, Personnel commitment and less turnover, Enhanced employee skills, With company and the economy constantly existing in a state of flux, Kaizen can be used throughout all sectors to yield little consistent enhancements.
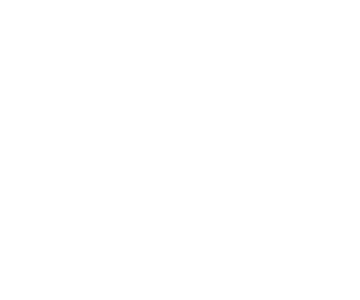
The 45-Second Trick For What Is Kaizen And How It Can Help You - Bit Blog
We're enrolling for the summertime! Discover more about or and.
A typical Kaizen occasion goes something like this: Set objectives and supply any necessary background. Review the existing state and establish a strategy for improvements. Carry out enhancements. Review and repair what does not work. Report results and determine any follow-up products. This type of cycle is regularly described as PDCA (Strategy, Do, Check, and Act).

Home - The Kaizen Company
More About 5 Massive Reasons Why You Should Conduct 5S Kaizen in
Kaizen, a Japanese word for "improvement", is often utilized in organization environments to implement and improve standardized activities & procedures. Introduced by Toyota after World War II, kaizens have now ended up being common practice in the manufacturing industry to constantly improve approaches or treatments that increase efficiency, eliminate waste, and/or minimize costs.